LEAN SAVJETOVANJE
Uvođenje Lean metodologije
(Toyota Production System® Just In Time)
NAJBRŽA ISPORUKA, NAJBOLJA KVALITETA, NAJMANJI TROŠAK
“Out of clutter find simplicity. From discord find harmony. In the middle of difficulty lies opportunity.” ― Albert Einstein.
Lean savjetovanje
Lean razmišljanje je opće prihvaćena metodologija kontinuiranog poboljšanja koja može uvelike pojednostaviti načine rada i poboljšati performanse u proizvodnim i uslužnim organizacijama. Lean pomaže organizacijama sagledati tokove stvaranja vrijednosti i procese s aspekta što zaista dodaje vrijednosti, a što je otpad.
Koristeći ključna načela, alate, tehnike Lean-a, pomažemo Vam u prepoznavanju i uklanjanju 8 otpada te poboljšanju produktivnosti. Kontaktirajte nas i prezentirajte nam Vaše probleme i izazove kako bismo Vam mogli predočiti potencijal učinkovite primjene Lean principa za Vaš konkretni slučaj.
Lean (Toyota Production System)
Lean metodologija je nastala iz Toyota Production System Methodology® (TPS), na temelju Just In Time (JiT) filozofije upravljanja proizvodnjom i procesima. TPS je nastao 1954 godine, a osnove je postavio Sakichi Toyoda, a dodano razvio Kiichiro Toyoda. Sustav se unaprjeđuje, ali osnove koje su postavili su do danas aktualne. IZ TPS-a su nastale metodologije poput Lean, Agile, Scrum, Six Sigma (MDAIC) metodologija.
Cilj Lean metodologije: Ostvariti ciljanu količinu najefikasnije, s najboljom kvalitetom i uz najmanji trošak.
Lean metodologija temelji se na 4 osnovne komponente: (1) Poslovnoj filozofiji = Motivaciji i zadovoljstvu svih shareholdera, (2) Standardizaciji = preduvjet automatizacije i JiT filozofije, (3) Pull logikom procesa = povlačenjem rezultata prethodnih procesa i (4) Kaizen/Jidoka – stalnim nadzorom i unaprjeđenjem standarda i procesa ODMAH I U TRENUTKU KADA SE UOČI NEDOSTATAK.
TPS (odnosno Lean) je cjelovita metodologija upravljanja poslovanjem koja uključuje sve shareholdere u jedinstvenu poslovnu cjelinu. Indikator uspjeha primjene TPS-a u nekoj tvrtki prepoznaje se po motivaciji i zadovoljstvu (poslovnoj kulturi) svih shareholdera, gdje svaki vlasnik i zaposlenik znaju zašto rade u svojoj tvrtki, a kupac i dobavljač s tom tvrtkom.
Six Sigma
Six Sigma (DMAIC) je razvijena 1970 u SAD-u na temelju TPS. Ona kombinira strukturirane korake (Define; Measure, Analyze, Improve, Control) i statističke metode za detekciju, analizu, uklanjanje i kontrolu defekata u procesima. Six Sigma sadrži i DMADV (or DMEDI) (Define, Measure; Analyze; Design; Verify) za dizajn novih procesa za nove produkte, servise. Six Sigma također koristi VSM ali za manje poslovne segmente i unaprjeđenja procesa. Six Sigma zahtijeva odlično poznavanje statističkih metoda i alata u cilju ispravne detekcije i definicije defekta te njihovog utjecaja na konačni ishod.
Six Sigma DAMIC je strukturirana procesno orijentirana metodologija koja daje najbolje rezultate kada su procesi barem djelomično digitalizirani, odnosno u nekom od IT sustava. .
Lean Six Sigma (LSS)
Lean Six Sigma nastaje krajem prošlog stoljeća, a značajniju primjenu ima od 2005. do danas. LSS kombinira prednosti obje metode. Lean metodologijom proširuje poslovni zahvat, a strukturirani pristup koristi od SIX SIGMA DMAIC metodologije.
Lean metodologija zahtjeva iskustvo i cjelovito sagledavanje problema koji se želi riješiti, Six Sigma zahtjeva odlično metodičko i statističko znanje koje će prepoznate probleme iz Lean metodologije uobličiti u konkretne podatke i pokazatelje. Lean metodologija u korekciji nedostataka (waste – defect) koristi soft metode (KANBAN, HENSEI; POKA-YOKE; HEIJUNKA, GENBA, GENCHI GENBUTSU, JIDOKA, 5S, KANO,…) koje primarno djeluju na kulturu rada i odgovornosti u tvrtki, Six Sigma primarno djeluje na IT podržane procese i automatizaciju procesa (materijalne izmjene u procesima) i KPI-jeve.
Svaki projekt je individualan, sukladno potrebama i izazovima oganizacije, no neki od pristupa koji su načelno mogući su slijedeći:
Implementacija jednostavnog rješenja za poznati problem u organizaciji.
Problem je jasan i ograničen na jedan odjel (organizacijsku jedinicu).
Način rješavanja: „Just Do It”.
Implementacija unaprjeđenja procesa i uklanjanja defekata korak po korak (DMAIC), gdje je problem poznat, a uzrok nepoznat.
Uzrok problema se identificira se tijekom projekta. Uklanjanje uzroka defekata (problema) i implementacija rješenja može biti jednostavno ili komplicirano (kros funkcionalno).
Način rješavanja: DAMIC metodom određuje se utjecaj defekta na poslovanje (FMEA), odrede prioriteti i način provedbe uklanjanja defekata.
Izrada i implementacija novih procesa za nove proizvode ili usluge.
Na temelju postavljenog cilja (količine proizvoda) definira se proces usklađen s resursima i drugim procesima.
Način rješavanja: DMADV metodom dolazi se do optimalnog procesnog tijeka s ciljanom količinom proizvoda u vremenu.
Implementacija nadzora / kontrole uspješnosti provedenih unaprjeđenja procesa.
Problem je što se ovaj dio provedbe projekta često „zaboravlja”, što kasnije uzrokuje povratak na stanje prije unaprjeđenja.
Način rješavanja: U ovisnosti u stupnju digitalizacije provedba se radi pomoću IT sustava ili edukacijom/coachingom voditelja odgovornih za pojedini segment procesa i izvješćima..
Lean metodologija
Lean metodologija je nastala iz Toyota Production System Methodology® (TPS), na temelju Just In Time (JiT) filozofije upravljanja proizvodnjom i procesima. TPS je nastao 1954 godine, a osnove je postavio Sakichi Toyoda, a dodano razvio Kiichiro Toyoda. Sustav se unaprjeđuje, ali osnove koje su postavili su do danas aktualne. IZ TPS-a su nastale metodologije poput Lean, Agile, Scrum, Six Sigma (MDAIC) metodologija.
Cilj Lean metodologije: Ostvariti ciljanu količinu najefikasnije, s najboljom kvalitetom i uz najmanji trošak.
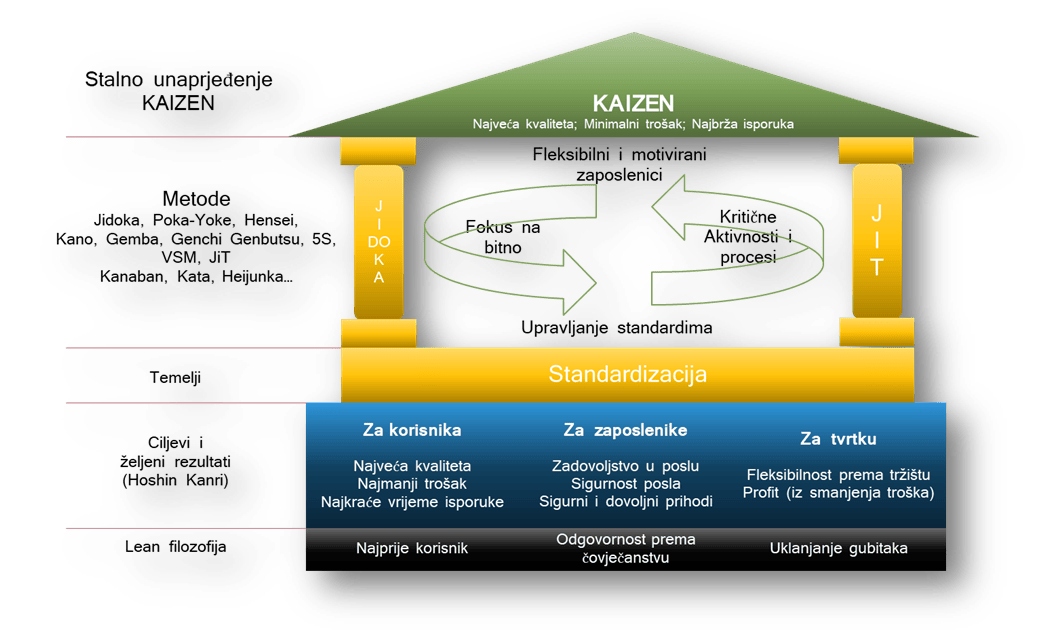
Lean metodologija temelji se na 4 osnovne komponente:
(1) Poslovnoj filozofiji = Motivaciji i zadovoljstvu svih shareholdera,
(2) Standardizaciji = preduvjet automatizacije i JiT filozofije,
(3) Pull logikom procesa = povlačenjem rezultata prethodnih procesa i
(4) Kaizen/Jidoka – stalnim nadzorom i unaprjeđenjem standarda i procesa ODMAH I U TRENUTKU KADA SE UOČI NEDOSTATAK.
TPS (odnosno Lean) je cjelovita metodologija upravljanja poslovanjem koja uključuje sve shareholdere u jedinstvenu poslovnu cjelinu. Indikator uspjeha primjene TPS-a u nekoj tvrtki prepoznaje se po motivaciji i zadovoljstvu (poslovnoj kulturi) svih shareholdera, gdje svaki vlasnik i zaposlenik znaju zašto rade u svojoj tvrtki, a kupac i dobavljač s tom tvrtkom.
Implementacija metodologije postavljanja realnih i balansiranih ciljeva na temelju stvarnih mogućnosti kompanije:
(1) Heijunka – sposobnost isporuke/proizvodnje,
(2) Jidoka – Razine automatizacije procesa,
(3) Poka Yoke – Kvalitete isporuke ili proizvoda.
Usklađenje ciljeva u slučaju promjena okolnosti (1.2 ili 3).
Pouzdan način postavljanja USKLAĐENIH ciljeva i propagacija prema svim zaposlenicima.
Uvođenje i implementacija standarda, identifikacija potrebnih resursnih kapaciteta (ljudi, alata, strojeva) koji su uključeni u izvršavanje procesa. Metodologija uključuje i vanjske partnere/dobavljače i njihovu sposobnost isporuke.
Heijunka osigurava optimalne resurse za ciljanu isporuku (proizvodnju), Stvara pretpostavke za optimizaciju i automatizaciju procesa. Ključna za postizanje cilja iz Hoshin Kanri.
„Automation with human touch”
Implementacija (dizajn, reinženjering, redizajn, automatizacija) maksimalno efikasnih procesa koji će osigurati tražene količine isporuke (proizvodnje) uz minimalne gubitke. Procesi su orkestrirani i standardizirani kroz cijeli vrijednosni lanac.
Jidoka osigurava smanjenje gubitaka nastalih zbog zaliha, čekanja, zamjene proizvodnje, prekomjerne administracije, nepotrebnog transporta i drugih poslova.
Uvođenje i implementacija standarda, identifikacija potrebnih resursnih kapaciteta (ljudi, alata, strojeva) koji su uključeni u izvršavanje procesa. Metodologija uključuje i vanjske partnere/dobavljače i njihovu sposobnost isporuke.
Heijunka osigurava optimalne resurse za ciljanu isporuku (proizvodnju), Stvara pretpostavke za optimizaciju i automatizaciju procesa. Ključna za postizanje cilja iz Hoshin Kanri.
„Mistake-Proofing”
Implementacija prevenira nastanak i uklanjanje višestrukih grešaka u konačnom „proizvodu” ili usluzi uz minimalne gubitke u produktivnosti ili efikasnosti. Reklamacije i dorade bi uzrokovale puno veće gubitke.
Značajno smanjuje gubitke nastale zbog reklamacija, ponovne isporuke ili proizvodnje. Na taj način osigurava pravovremenu isporuku u količini i kvaliteti. Povećava zadovoljstvo korisnika.
Implementacija osigurava postavljanje radnog okruženja za maksimalno efikasnu proizvodnju, logističke usluge ili isporuku usluga. Postavlja set pravila koja osiguravaju da svako radno mjesto ima pravovremeno dostupne sve resurse potrebne za izvršenja zadataka.
Značajno smanjuje gubitke nepotrebnih radnji (motion waste) i neproduktivnih radnih mjesta. Smanjuje gubitke prilikom zamjene smjena i zamjene proizvodnje proizvoda.
„Mistake-Proofing”
Implementacija prevenira nastanak i uklanjanje višestrukih grešaka u konačnom „proizvodu” ili usluzi uz minimalne gubitke u produktivnosti ili efikasnosti. Reklamacije i dorade bi uzrokovale puno veće gubitke.
Značajno smanjuje gubitke nastale zbog reklamacija, ponovne isporuke ili proizvodnje. Na taj način osigurava pravovremenu isporuku u količini i kvaliteti. Povećava zadovoljstvo korisnika.
Ispuniti očekivanja korisnika za količinom, kvalitetom i cijenom kontinuiranim (KAIZEN) unaprjeđivanjem svakog dijela vrijednosnog lanca do krajnjeg klijenta do postizanja najbrže isporuke, najbolje kvalitete i minimalnog troška.
Lean metodologija djeluje na trošak i količinu isporučenih proizvoda ili usluge na način da smanjuje trajanje proizvodnje/isporuke usluge po jedinici proizvoda/usluge, uz istovremeno zadržavanje kvalitete proizvoda. Just In Time princip osigurava da dobavni lanci ugradbenog materijala, ili robe za isporuku dolaze u vrijeme i u količini koja je u skladu s sposobnostima isporuke/proizvodnje pojedine faze, prevenirajući stvaranje velikih zaliha.
Lean metodologija gore navedeno postiže kvalitetnim planiranjem (Hoshin Kanri), optimalnim kapacitetima (Heijunka) i optimalnim odnosom učinaka čovjeka i alata s kojima radi (Jidoka). Kvaliteta i uspješnost provedbe se postiže se Poka Yoke metodom minimalne greške, 5S metodom kvalitete radnog mjesta i Gemba metodom vođenja operativne proizvodnje/isporuke.
Najbolje i najuspješnije tvrtke u svijetu su primijenile Lean metodologiju u cjelini (Google, Toyota, Kyocera, Lego, Allseas, DM, Unilever, DHL…) i one imaju trajni održivi rast i stabilnost. Neki žele kratkoročne benefite i nisu spremni uvoditi Lean u cjelini u određenom trenutku. I to je moguće ali rezultati će dolaziti sporije, a financijski učinci će biti znatno manji.
Uspješnu primjenu ovih metoda Lean osigurava djelovanjem na sva tri shareholdera: kupca, vlasnika i zaposlenika. Za to je potrebno je prihvatiti Lean filozofiju (korporativnu kulturu) u cjelini, uvoditi je u koracima u skladu s prioritetima i redoslijedom uvažavajući posebnosti organizacije. Drugi važan element u primjeni Lean metodologije je STANDARDIZACIJA. Da biste napravili dobar odnos između čovjeka i stroja/alata (Jidoka) potrebno je standardizirati način rada, procesne inpute i outpute (KANBAN) i kapacitete (Heijunka). Tek kada ste to napravili moguće je krenuti prema optimizaciji vrijednosnog lanca do korisnika. Prilikom optimizacije djelujemo na tri elementa: na mikro procese, način rada (kompetencije,…) ili na standarde. Ispravnom identifikacijom uzroka (Ishikawa) možemo doći do optimalnih rješenja s minimalnim ulaganjem i ostvarenjem zadanog cilja.
Neke tvrtke ( u Hrvatskoj) su povećale učinkovitost 3 puta. To znači da su nakon primjene Lean metodologije bile su u stanju isporučiti 3 puta više proizvoda/usluga u istom periodu nego prije, uz manje reklamacija i s istim ili manjim resursima. To se odrazilo na povećanje prihoda i dobiti, povećanje zadovoljstva kupca smanjenim rokom isporuke uz povećanje kvalitete. Uvođenjem transparentnosti (dnevni uvid u učinke) u model nagrađivanja povećalo se zadovoljstvo zaposlenika.